"The Subfloor System produces an overall lighter construction and improved economy."
For In-Situ construction using the Subfloor system, the base substrate can be cast thinner. This maintains the sound insulation quality or can be improved with our acoustic feet and insulation bearers.
Subfloor systems are commonly installed on hollow core slabs when the objective is to attain sound class A or B for dwellings without additional topping.
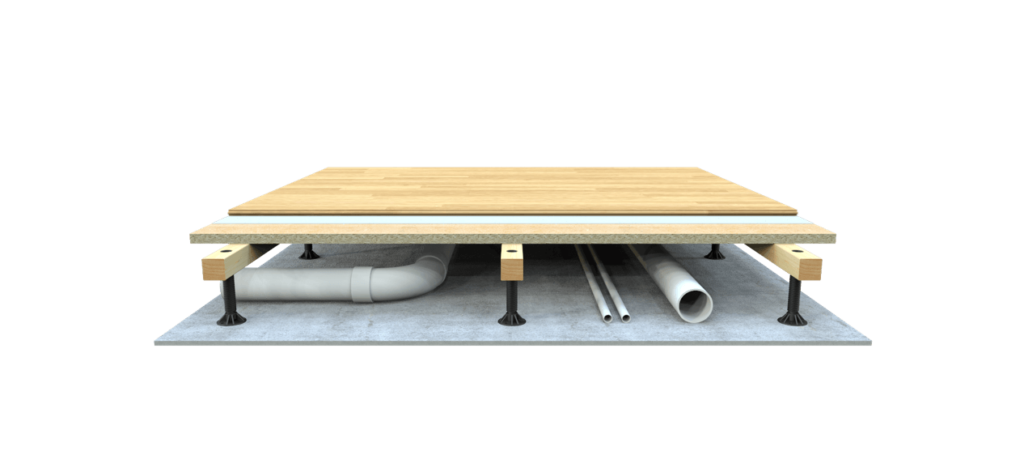

SubFloor systems can be installed directly on wooden floors so as to achieve improved impact and airborne sound insulation for the overall construction.
Quick, quiet and clean installation
Adapted for high load requirements
A multi-purpose system - Acoustic, ventilation, installation and decking


Less CO² impact than concrete
Construction heights from 11 - 398 mm
Low weight and adaptable installation space
Assembly
Typically an assembly team of two people is recommended.
Typical assembly speed: Larger room, Subfloor System = 20 - 24 m2 an hour.
Slow grown pine with low moisture content means minimal warping and a dense grain structure for a high load tolerance.
Attachment Methods
Glue - Apply suitable glue between substrate and screw foot
Screw/plug (with foot) - fix a nail/screw/plug through the base plate on the screw foot
Screw/plug (without foot) - Drill through the screw and attach the screw with wood screws/plug
Acoustic Damping
Acoustic feet - reduce impact noise up to 28 dB
Hanging insulation bearers reduce airborne noise without contact
Dampens vibrations regardless of load and floor angle due to acoustic foot rubber design
Joist Options
Steel joists - 11 and 30 mm high
Wooden joists - 45, 70 and 120 mm high
Pressure-treated joists - 45 and 70 mm high