SubFloor Acoustic Raised Access Flooring Revitalises an Office space at Barnsley Civic
SubFloor acoustic raised flooring was used to renovate, raise and level a 282 m² floor into a modern office space above a theatre in Barnsley.
System: SubFloor Acoustic Raised Access Floor System
Products:
Wooden Joist 45 x 70 x 3600 mm
Subfloor Screw 300 mm
Screw Foot Acoustic 25
Construction:
Joist separation: c/c 600 mm
Building height: 112– 364 mm
Data:
System weight: 4.50 kg/m²
Acoustic damping: Up to 28 dB [rating according to ISO 717-2]
Point Load 50 x 50 mm: 5.78 kN
Uniformly Distributed Load:
10.6 kN/m² - Between screws
15.3 kN/m² - Over screw at joist edge
[According to SS-EN 1195:1998]
Materials:
Pine T0-C24
Fibre-reinforced Vitamide
Polyamide + Thermoplastic Elastomer
Introduction:
This case study highlights the successful renovation of a space above a theatre into offices in Barnsley, focusing on the integration of the SubFloor Raised Access Floor system. The project, developed by HLM Architects and constructed by Code Building Solutions, required careful attention to acoustic requirements, impact noise reduction, and vibration damping. The SubFloor system, featuring acoustic feet and reinforced construction components, offered an ideal solution for meeting these challenges while ensuring simplicity, speed, and efficiency during assembly. Testimonials from contractors further attest to the system's ease of installation.
Project Overview:
Location: Barnsley, United Kingdom
Project Type: Renovation of space above a theatre into offices
Floor Space: 282 m²
Requirements: Acoustic damping, substantial floor height increase, level installation on top of an old wooden floor
Challenges:
Acoustic Damping: Meeting acoustic requirements for sound insulation between the offices and surrounding spaces, while effectively reducing impact noise and addressing issues related to rebound noise and flanking transmission.
Raised Floor Height: Accommodating a significant height increase of up to 350 mm to achieve a level installation on top of an existing uneven wooden floor.
Simplicity and Speed: Choosing a flooring system that allowed for quick and efficient assembly, without compromising on quality or compliance with load-bearing requirements.
Solution: SubFloor Raised Access Floor System
The SubFloor Raised Access Floor system, selected for this project, provided an effective solution to meet the specific requirements of the renovation.
1. Acoustic Performance:
The integration of acoustic feet within the SubFloor system played a crucial role in achieving the necessary acoustic performance. These acoustic feet not only helped dampen impact noise but also assisted in mitigating rebound noise and flanking transmission, ensuring a quieter and more controlled office environment. The system effectively reduced sound transmission between the offices and surrounding areas, promoting productivity and privacy.
2. Height Increase and Level Installation:
The SubFloor system accommodated the substantial height increase of up to 350 mm required for the project, allowing for a level installation on top of the existing uneven wooden floor. This capability provided a smooth and uniform surface for the subsequent application of floor coverings.
3. Reinforced Construction Components:
The SubFloor system utilized fibre-reinforced screws and slow-grown Swedish pine, ensuring the system met all load-bearing requirements. The use of high-quality construction materials enhanced the structural integrity of the raised access floor, supporting its long-term durability and reliability.
Assembly Process and Testimonials:
Contractors involved in the project were impressed with the simplicity and efficiency of the SubFloor Raised Access Floor system. They commended the ease of installation, with one contractor noting that "a child could have built it". This positive feedback further validated the system's assembly ease and its ability to meet the specific needs of the project.
Additional Acoustic Measures:
To augment the acoustic performance, 22 mm chipboard was assembled on top of the SubFloor system. This layer contributed to meeting the project's acoustic requirements and provided a stable foundation for a variety of floor coverings, allowing for customization based on aesthetic preferences and functional needs.
Conclusion:
The renovation project above the theatre in Barnsley, developed by HLM Architects and constructed by Code Building Solutions, successfully integrated the SubFloor Raised Access Floor system to meet the acoustic damping, height increase, and level installation requirements. The system's acoustic feet effectively reduced impact noise, rebound noise, and flanking transmission, creating a productive and comfortable office environment. The inclusion of fibre-reinforced screws and slow-grown Swedish pine ensured the system's compliance with load-bearing requirements. Contractors praised the simplicity and efficiency of the assembly process, reaffirming the system's suitability for architects and contractors in the construction industry. The SubFloor system proved to be a reliable and effective solution for achieving superior acoustic performance and efficiency in office renovations.
Project Gallery
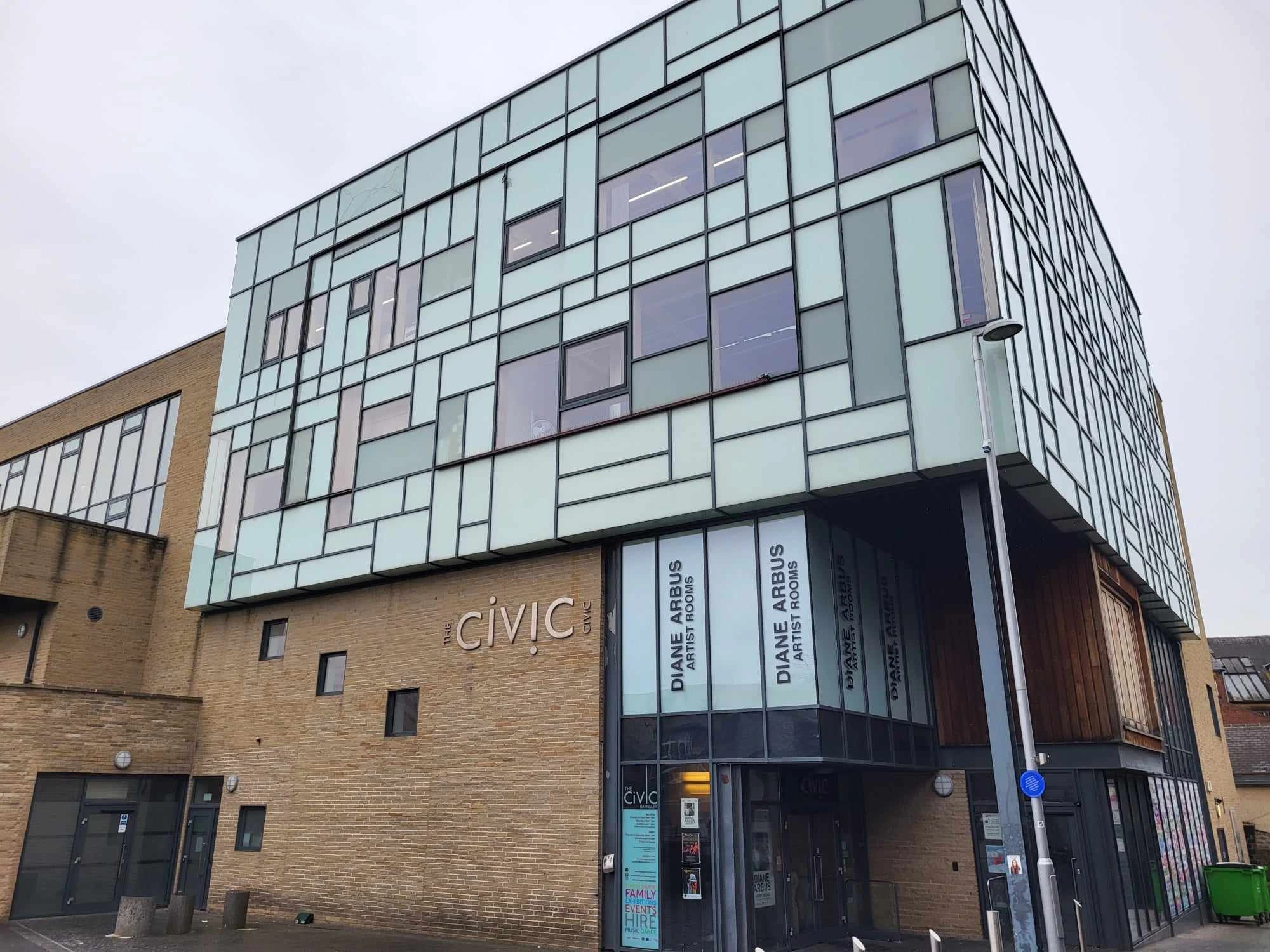
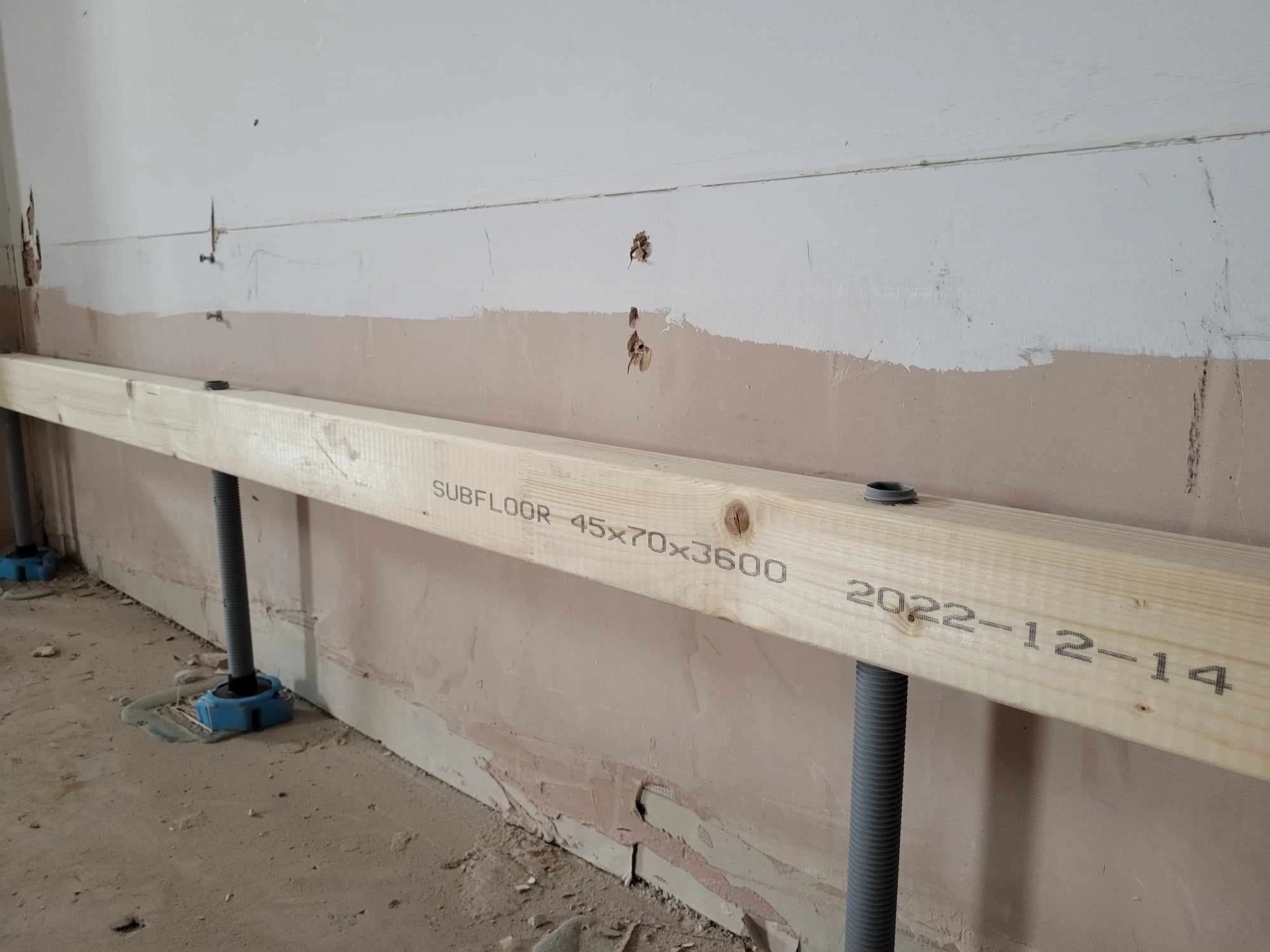
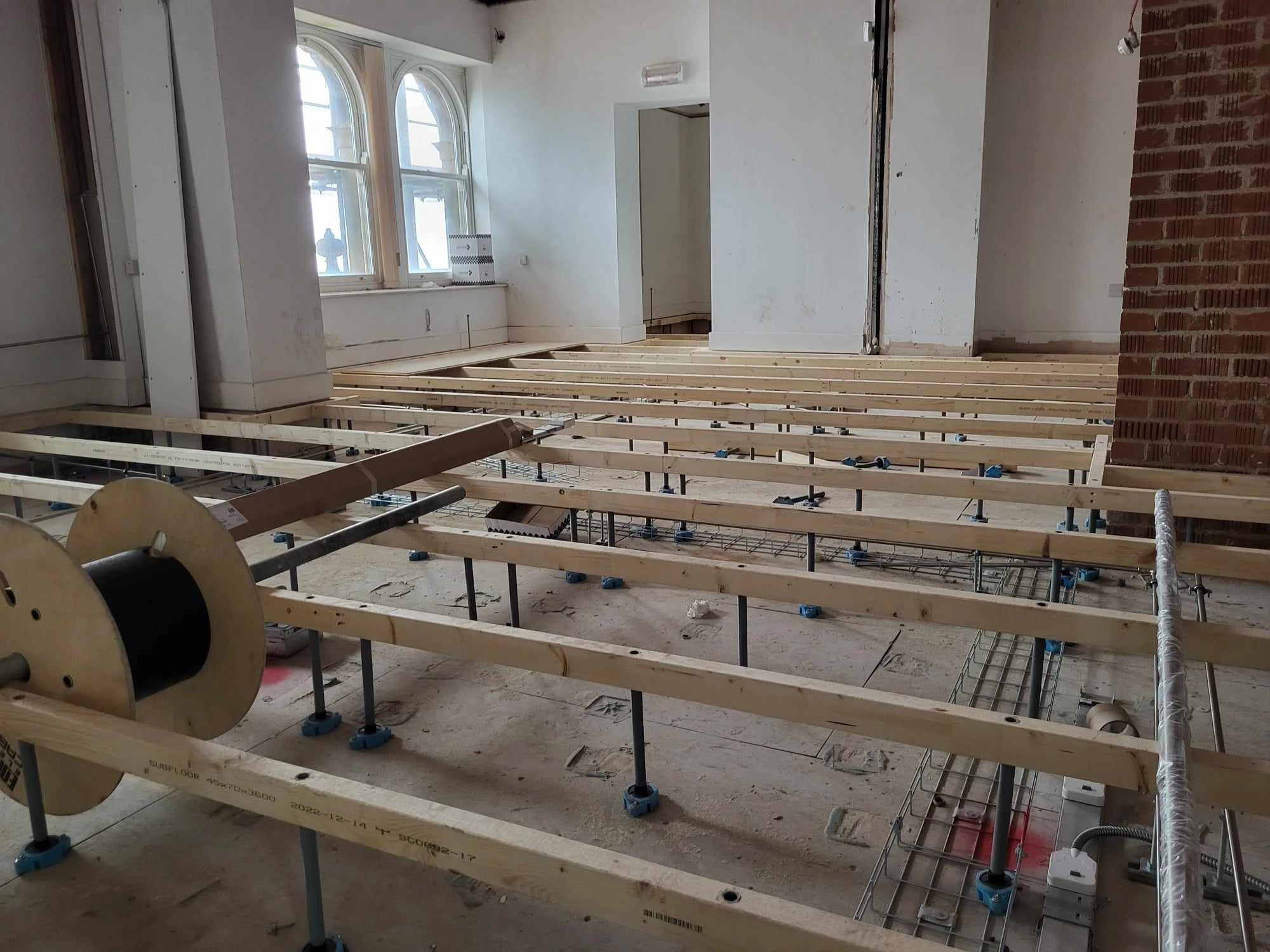
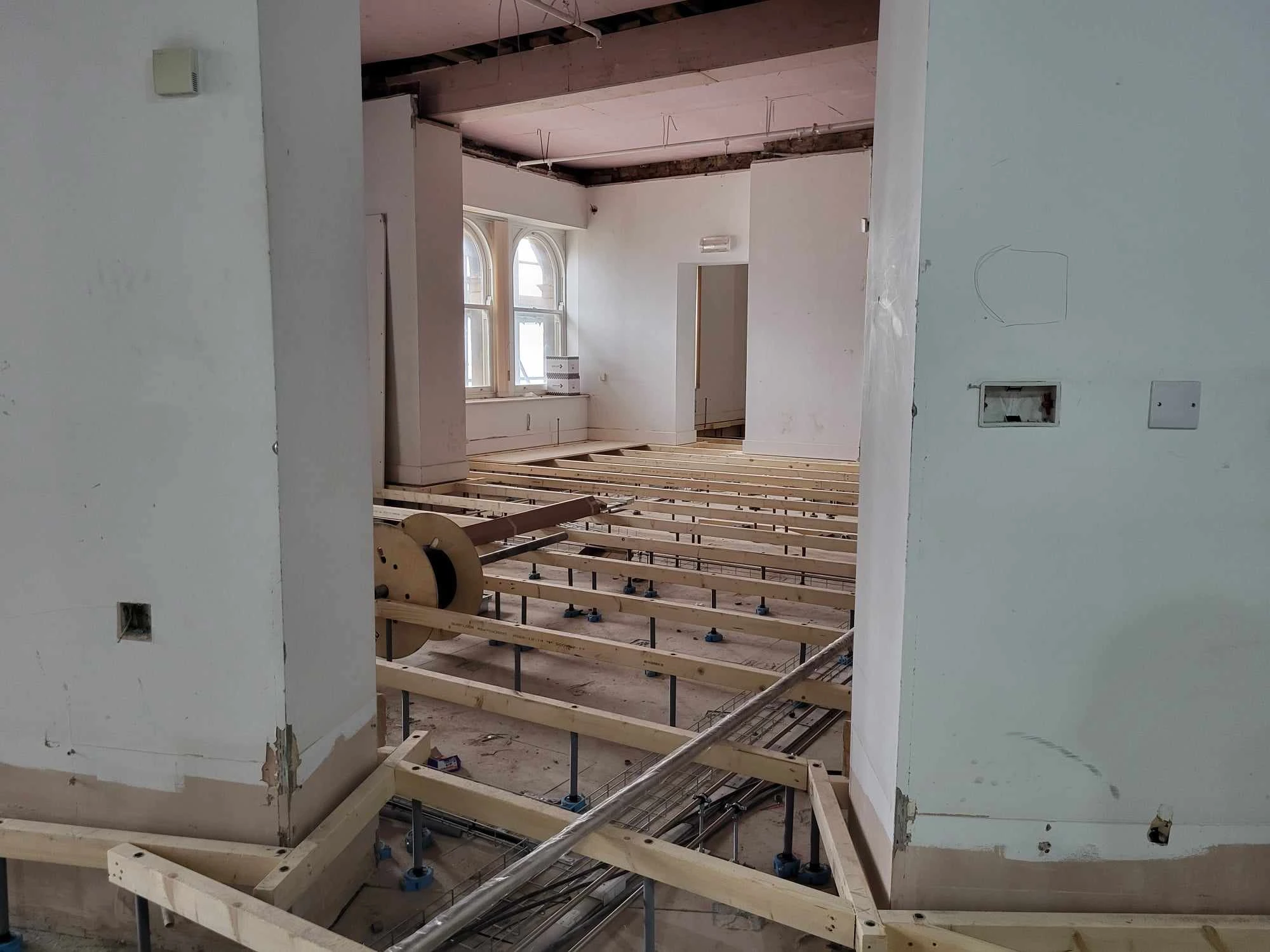
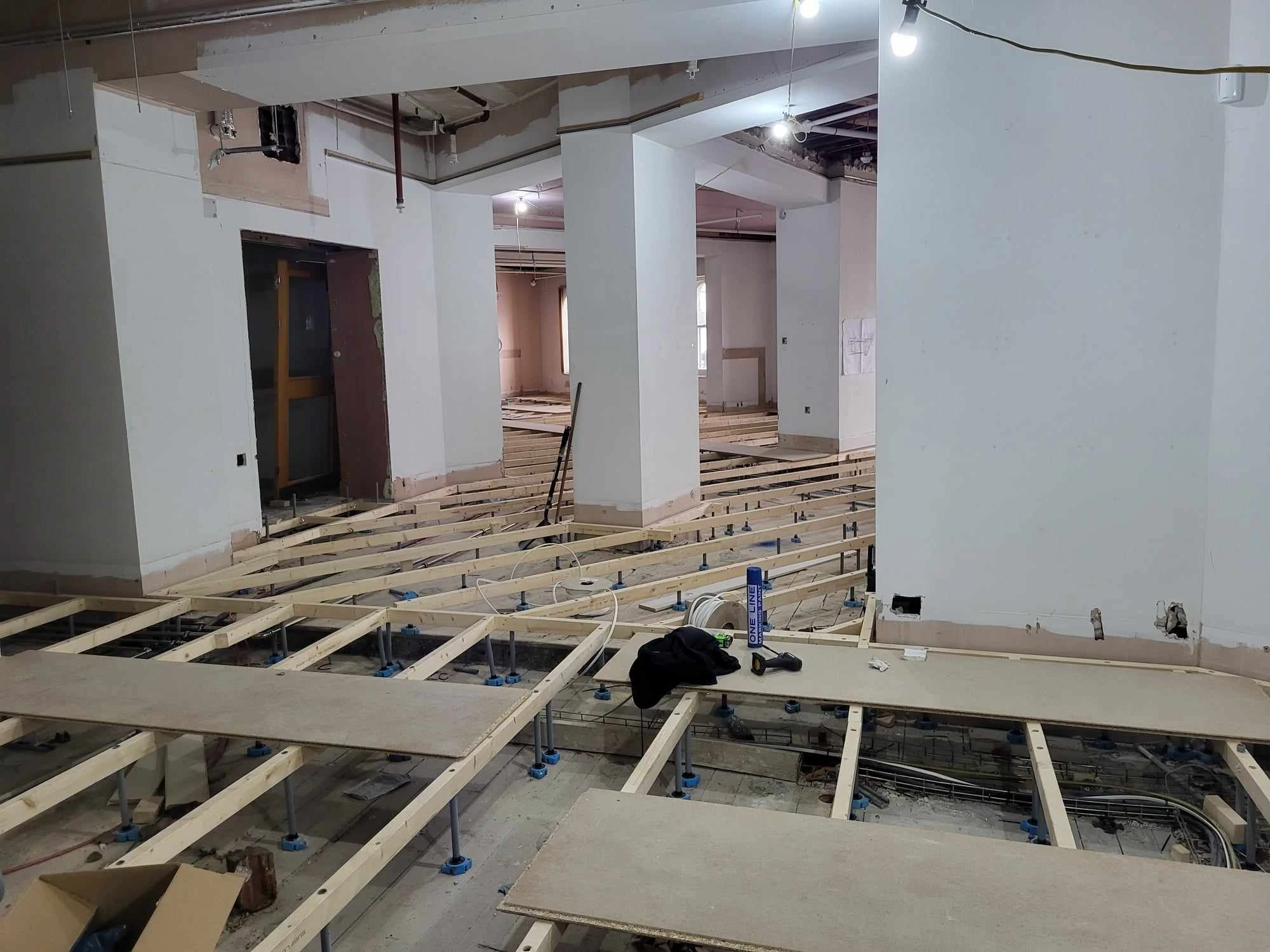
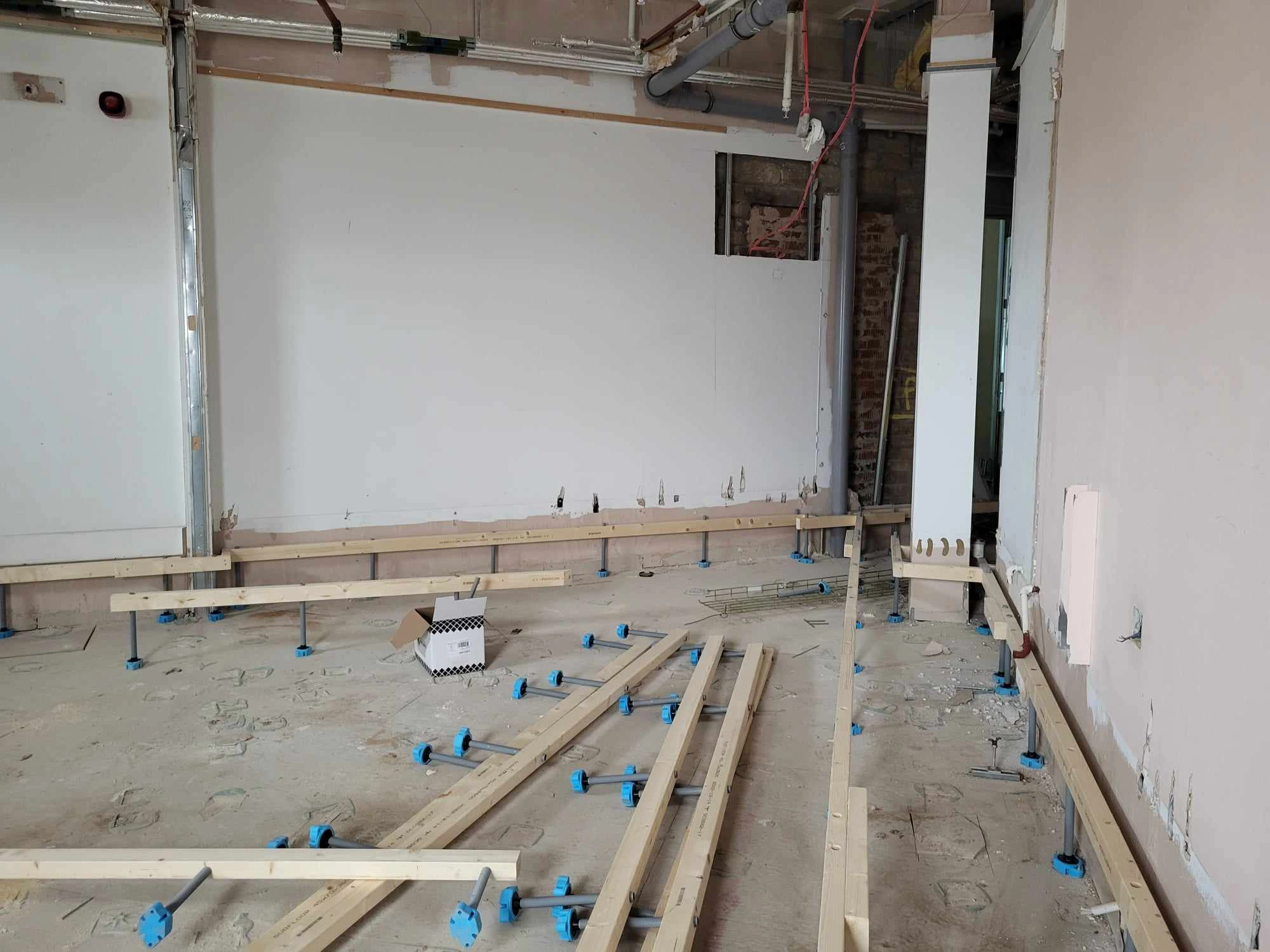
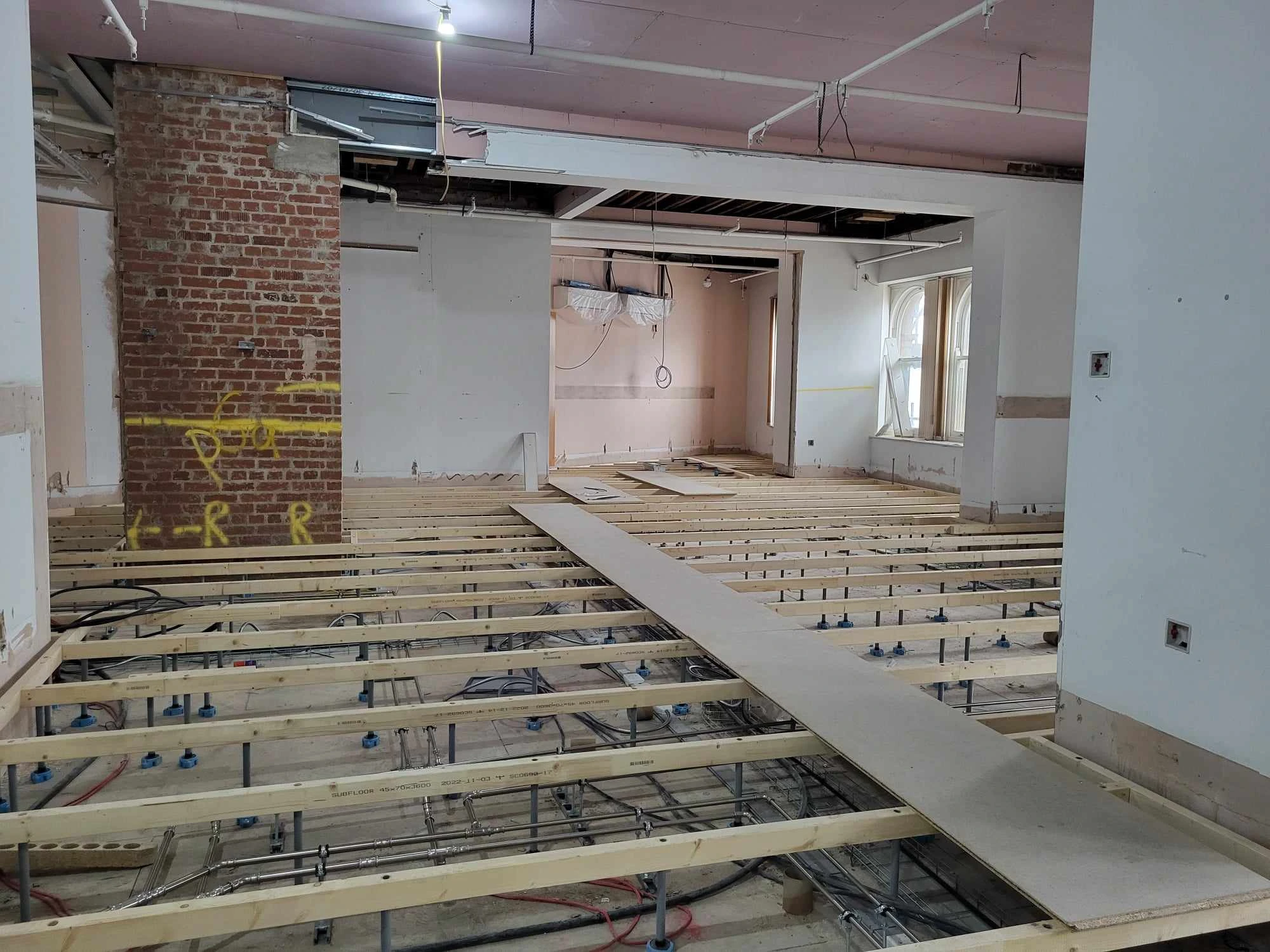
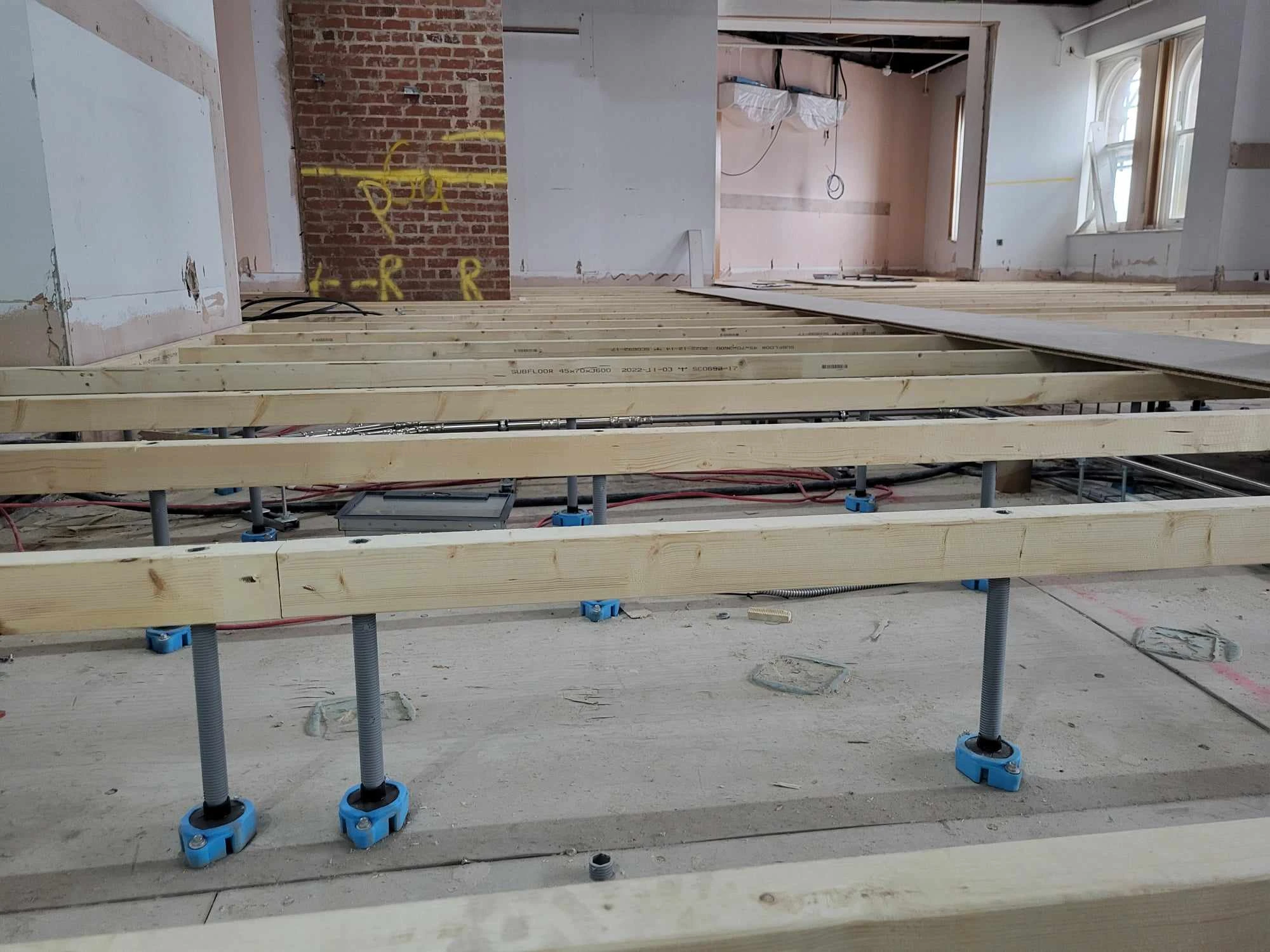
Some of our other SubFloor projects…
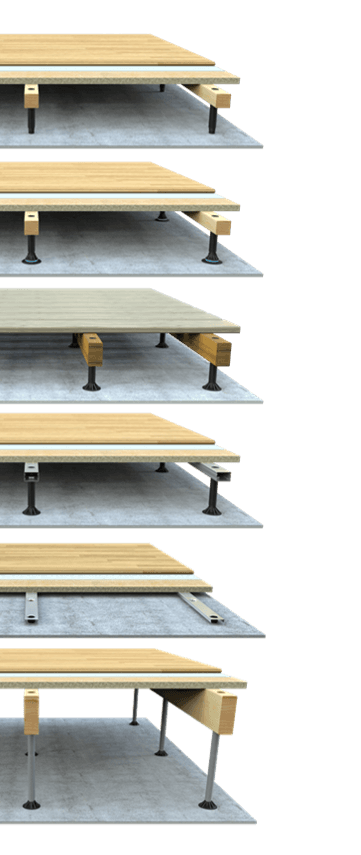